Fall Protection – Critical Safety for Working at Heights
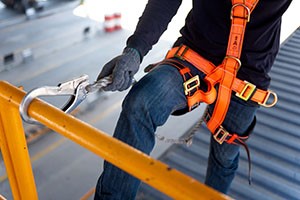
Safety continues to be a major concern in the construction, industrial cleaning, and oil and gas industries around the country in which people work at heights. Workers face a multitude of hazards on the job daily.
Safe work practices and ongoing training are crucial when protecting workers from devastating falls. By knowing what equipment is needed on the job site, providing that equipment to the crew, and training them how to properly use it, employers can help prevent injuries and deaths.
The first step is to identify fall hazards and decide how to provide the best protection. Analyzing the work area may include reviewing blueprints before work begins, anticipating upcoming fall hazards as work progresses, looking at current hazards, and preparing a pre-planning checklist.
There are many ways to protect workers from falls, including using guardrail systems, safety net systems, and personal fall arrest systems (PFAS).
Know the ABC’s
The basics of every PFAS is commonly described as the ABC’s of fall arrest:
A – Anchorage: A secure point of attachment (structure) for the fall arrest system.
B – Body Support: Full body harnesses provide a connection point on the worker for the personal fall arrest system.
C – Connectors: Devices used to connect the worker’s full body harness to the anchorage system (ie. shock absorbing lanyard, self-retracting lifeline, etc.). Self-retracting lifelines (SRLs) keep workers safe at any height. Most SRLs stop falls within 24”. Crew members don’t have to calculate the fall distance when using an SRL, as opposed to a lanyard.
D – Descent/Rescue: Rescue and retrieval of a fallen worker is a required component of any fall protection program.
Individually, these components won’t provide protection from a fall. However, when they’re used properly and in conjunction with each other, they form a PFAS that’s crucial for safety on the job site. Choosing this equipment should always be in accordance with the jobs performed, the job conditions, and the individual worker.
Crew members who are exposed to a fall must also be trained by a competent person on the correct procedures for set-up of the fall protection systems to be used, the use and operation of the equipment, their role, the limitations of the equipment, and proper handling and storage. By implementing safety procedures for crews, employers can help everyone stay injury-free.
Also inform employees that fall protection components are designed to be used with the same manufacturer's approved components and connecting subsystems. These manufacturers strongly recommend that workers using fall protection take full advantage of the functional compatibility built, tested, and approved within the same manufacturer's fall protection components. The compatibility of substitutions and the use of substitutions may jeopardize the safety and reliability of the complete system.
Equipment Inspection
Using equipment past its useful life is a potentially deadly mistake. Fall protection equipment must be inspected regularly and taken out of service if if it has been involved in a fall or it shows signs of wear. Wear can be caused by daily use or exposure to heat and chemicals. A few signs a worker should look for before using their equipment are fraying, cuts, and deformed metal hardware.
Increasing Compliance
When employers begin to select fall protection equipment, there are features to look for that may result in higher compliance. Choosing a harness with an ergonomic design and leg and shoulder padding relieves discomfort, leading to higher worker acceptance. For example, if a harness isn’t comfortable, then workers may take steps to make it more comfortable, like loosening the straps too much. However, an improper fit just doesn’t offer the same level of safety.