How Facility Maintenance Can Reduce Worker Injury
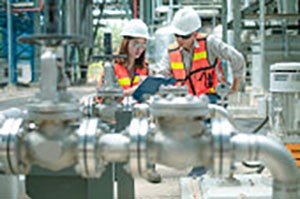
How can regular machinery maintenance equal greater worker safety?
Improperly functioning machinery puts workers at risk of injury or worse. Regularly scheduled maintenance in your facility and on your jobsite can help diminish the risk, with the added benefits of minimizing downtime and saving money.
Employees working on or near improperly maintained machines face a variety of hazards, from machinery-related incidents, to slips, trips, and falls. Those employees are not the only ones at risk, though. The risk of injury extends to the workers responsible for repairing the machinery. The most common injuries and fatalities linked to maintenance are:
• Falls from working at heights
• Confined spaces or harsh environments associated with accessing equipment
• Shocks and burns if power is not properly isolated
• Injuries from moving machine parts
• Musculoskeletal problems related to exerting force or working in awkward spaces
• Exposure to asbestos, chemicals, dust, and excessive noise
Three Categories of Maintenance
• Routine (preventative) maintenance is performed to keep equipment working, help it perform more efficiently, and extend its service life.
• Corrective maintenance gets broken or improperly functioning machinery running again.
• Predictive maintenance includes testing the equipment to determine if maintenance is needed, or will be needed soon.
No matter what type of maintenance is being performed, including oil changes, filter replacements, or fitting repairs, precautions must be made to ensure safety. Skipping these steps is dangerous for workers and the jobsite.
• Maintenance procedures must be developed for all equipment, and should follow manufacturer recommendations.
• Maintenance activities should be planned, even emergency repairs.
• Maintenance workers must be trained on the equipment they’re working on.
• Maintenance workers must be properly protected with safety equipment, including gloves, eye protection, and hard hats.
• All sources of electrical power to the equipment being maintained must be disconnected and tagged “OFF” to ensure the power is not turned on while work is being completed. The machine under repair must also be isolated from all others on the same system, and a proper lockout/tagout device must be employed. Failure to do so can result in electric shock, electrocution, fire, or explosions.
• Hydraulic pressure is released and equipment is in a relaxed position.
• Any safety devices (machine guards, shields, etc.) removed during maintenance must be reinstalled before maintenance is complete.
• Before the machine is put back into service, repair work should be inspected by a supervisor familiar with the equipment. This will ensure the maintenance is complete and the equipment has been properly reassembled.
The Importance of Recordkeeping
Logging inspections, maintenance, and repairs has benefits for operators and supervisors alike. Recurring issues, like an elbow that continuously cracks, may require further investigation or a different method of repair. You can easily see from a log book if equipment is requiring more fluid than normal, possibly indicating that there is a problem, like a leak in the hose. Finding solutions ahead of time reduces machine downtime, helps in budgeting, and assists in overall scheduling and production.