Using Leading Indicators to Improve Safety and Health Outcomes
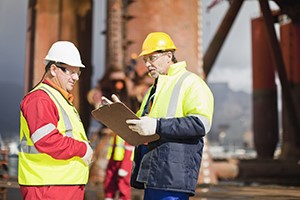
Leading indicators can play an important role when trying to increase safety in the workplace. They are proactive and preventative measures that shed light on the events leading up to injuries, illnesses, and other workplace incidents and reveal other potential problems your health and safety programs may have. A popular leading indicator is weekly hours worked, because it allows employers to get an idea if their workers are being overworked, which may increase the chance of injury or illness.
Along with leading indicators, employers also use lagging indicators. They measure the occurrence and frequency of events that occurred in the past, such as the number or rate of injuries, illnesses, and fatalities. Lagging indicators alert you to a failure or hazard in your safety and health program, while leading indicators are designed to minimize failures in your safety and health programs.
A good safety and health program uses leading indicators to drive change and lagging indicators to measure effectiveness. The Campbell Institute states:
Today, EHS practitioners continue to rely on injury rates, absenteeism, and other lagging metrics despite the growing acceptance of the fact that these failure focused measures are ineffective in driving continuous improvement efforts. Leading indicators, on the other hand, appear to offer a more useful gauge of EHS activity by providing early warning signs of potential failure and, thus, enabling organizations to identify and correct deficiencies before they mature into accidents and injuries.
Leading indicators can improve organizational performance by:
- Preventing workplace injuries and illnesses.
- Reducing costs associated with incidents.
- Improving productivity and overall organizational performance.
- Optimizing safety and health performance.
- Raising worker participation.
To download a leading indicator guide and find more resources, visit OSHA’s website.